Manufacturers of metal parts using 3D printing technology tend to use one of two methods: SLS (selective laser sintering) or SLM (selective laser melting). Each of these two technologies has its particular advantages, but relatively high cost and potential emissions of harmful substances are their common disadvantages. Now the Austrian company has developed a new metal 3D printing method that offers a cheaper and safer alternative. The technology is called FMP (Fiber Metal Printing) and the process was recently launched at the EVO-tech headquarters.
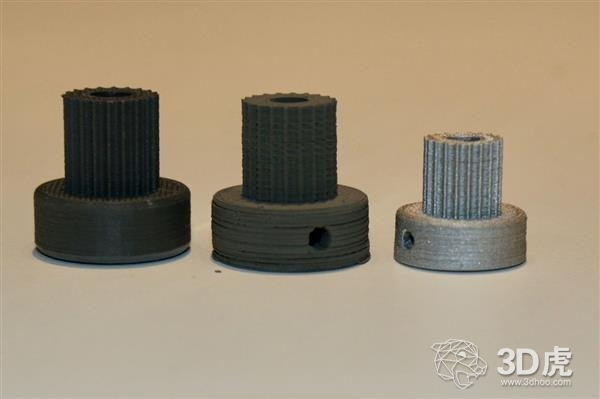
Filament metal printing is close to laser sintering because it uses a volume of metal powder that is selectively melted before resolidifying into the desired shape. EVO-tech's innovation is to first process this metal powder to form filaments, similar to the plastic filaments used in FDM or FFF 3D printing. The wire used in the extrusion process is already available, but unlike this, EVO-tech's technology is capable of producing parts that are as close to metal as metal powder.
After the metal powder is selected for the filament, a suitable binder material (usually a polymer) is mixed therewith. The resulting particulate material is then formed into filaments. The wire can be extruded through a nozzle under pressure and elevated temperature. So far, this step has been implemented using EVO-tech's EVO-lizer 3D printer, which is designed for processes with hardened, high temperature nozzles (up to 330 degrees Celsius) and high temperature print beds.
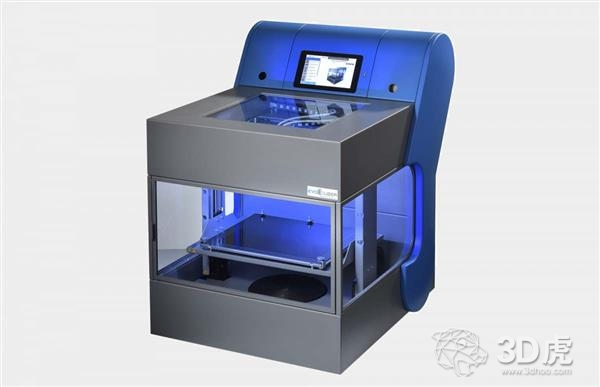
Parts produced during the extrusion process are referred to as "green parts." Once completed, the next stage is to remove most of the bonding material. There are various debinding methods such as thermal debonding, catalytic debonding or the use of solvents to remove the binder. The resulting "brown portion" will now become very fragile, consisting almost entirely of metal powder, which is loosely held together by any residual polymer residue. The final step is sintering, which removes the remaining polymer binder and shrinks the "brown portion" to form a stronger, stronger final product. Temperatures up to 1300 degrees Celsius are necessary to burn off plastic residues and shrink parts up to 20%.
The final product left behind is a precision manufactured high quality object with excellent material properties. A process similar to FMP is called powder injection molding. This also uses high sensitivity plastic bonding materials and the final sintering stage to produce metal parts.
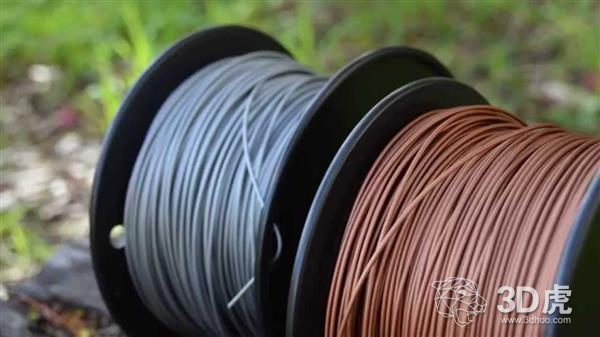
The main advantage of FMP is that it can 3D print metal parts with cavities. Now using the 3D printing method, it is easier to produce a cooling channel or honeycomb structure with a lighter structure. The lack of a metal powder bed means that the process does not emit harmful substances, so FMP 3D printers can be installed in a regular work environment like an office.
EVO-tech has mastered this technology for about a year and a half, and it has been developed with the support of German chemical giant BASF, and its influence on the 3D printing world is growing at a considerable rate. This technology is 90% cheaper than other metal 3D printing methods. This will enable the production of 3D printed metal parts to be more extensive and can be applied to a wide variety of applications in different industries.
When you have secure sports lockers to store personal belongings, it is easily for you to concentrate on your fitness goals.
It is frequently to see metal gym storage lockers because their low cost and fair durability and bespoke service.
Combining visibility and maximum air flow effectively with security,vented Metal Lockers are ideal choices of School Lockers of sports.
Z - Standard Metal Lockers are designed to withstand daily use and abuse for any school, gym, or dressing room.
Do not pay too much money for gym & althetic lockers online,you`d better look for a lockers manufacturer.
Sturdy Day Use Lockers,Durable Changing Room Lockers,Gym & Athletic Lockers Online
LUOYANG SHIDIU IMPORT AND EXPORT CO., LTD , https://www.ybshidiu.com