Gehl`s Guernsey Farms, based in Wisconsin, USA, offers home-style flavoured cream puddings for food and beverage outlets and retailers in a variety of packaging formats. Recently they have added a 3.5-ounce cup pudding, which has been used for decades for canned and re-sealable bags. Mr. John P. Gehl, CEO of the company, said: "We want to provide the best quality products and we also want to try all possible packaging."
Gehl uses a brand new aseptic filling line produced by Hassia () USA. Mr. Mike Sowieja, Gehl's Deputy Director of Engineering, said: "This filling line allows filling 10 chocolate flavors and 14 vanilla-flavored pudding cups at a time; or 12 cups per flavor for each operation, with two flavors interspersed; If necessary, it can also be mixed with taste filling, layer filling, and cup filling, 4 cups, 6 cups or 12 cups, and because the production and packaging process is completely automated, the operating cost is relatively low."
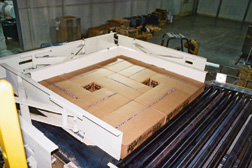
An automatic stacker above the ground transports the well-packed containers to a suitable location.
In order to form a new layer on the pallet.
This new packaging line includes four new Dynac vertical storage tanks produced by Hartness Intl. (), three Davis brand cartoners, and two packaged box loaders from Douglas Machine (). The Currie () tray machine and a rotary table stretch packer from Lantech () company are optimally configured to ensure the best product quality and maximum speed, and all of these require only two workers. The entire packaging line is integrated with the conveyors and consoles produced by Sentry Equipment ().
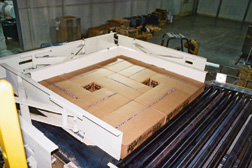
Place a separate aseptic molding/filling/sealing machine on its own
Easy to control temperature and other parameters.
A new measuring cup pudding complements Gehl`s original canned and bagged pudding packaging, offering an alternative to old customers. The main sales channel for new packaged products will be mainstream retailers, Mr. Gehl explained. “In the long run, customers who supply their own brands will be the main outlets for bulk products.â€
Gehl`s recently introduced this new set of equipment, Hassia's TAS type low acidity, steam anti-corrosion thermoforming/filling/sealing machine, with reference to the same equipment unit installed in the rival factory. Gehl said: "The difference is in operations," he added: "We feel that Hassia is the best company that can provide these devices."
Hassia TAS 16/80 is a sterile thermoforming/filling/seal system that was put into use at Gehl`s in February 2003. Its product width is up to 840mm and the production speed is 160mm per action. At Gehl`s company, the machine is horizontally arranged in two rows, each row is filled with 12 cups, so that each action can complete the task of filling 24 pudding cups, and can perform 28 filling operations per minute.
Unlike some other aseptic heat-setting/filling/sealing machines, this TAS 16/80 machine uses steam instead of hydrogen peroxide (hydrogen peroxide) to sterilize cup body and closure materials at room temperature. Save it. "With steam sterilization, you don't have to worry about hydrogen peroxide residue in the product," explained Jeffrey Martin, Gehl's special project manager, "Steam is a very clean disinfectant."
The new machine is placed separately so temperature and other parameters can be controlled. To take advantage of the versatility of the loader, Gehl`s installed two new aseptic storage tanks produced by Advanced Process Solutions (), each with a capacity of 3,000 gallons. The two tanks are responsible for transferring raw materials to the four buffer tanks of Hassia equipment, so that a series of pudding product combinations can be loaded at the same time. Although chocolate and vanilla-flavored products are currently being packaged, Gehl`s will also pack savoury cream, tapioca, chocolate and lemon-flavored puddings.
In order to prepare the pudding, pudding sauce was pumped from two 40,000-gallon storage tanks to a batch system. This system is also the product of APS. It first heated the pudding to a temperature for sterilization. - The chocolate taste is 281 degrees Fahrenheit, vanilla flavor is 276 degrees Fahrenheit - and then the pudding is cooled to 90 degrees Fahrenheit. At the end of this step, the pudding was transferred to a 3,000-gallon storage tank and from there the four buffer tanks of the filling machine were supplied.
This heat setting/filling/sealing process begins with the sheet material being used as the cup body material being pulled from the roll onto the machine. The upper end of the sheet is steam sterilized at 305.2 degrees Fahrenheit twice for 0.98 seconds each. . The body sheet is a five-layer material from Printpack (), which is a polyethylene layer/adhesive layer/oxygen barrier layer/adhesive layer/polyethylene layer from the inside out.
Next the cup body material enters the forming position where a stopper is first used to help the material to be preformed and then blown into the air to form a pudding cup. The molded pudding cup was sent to the filling machine. The filling machine used 24 loading heads to pack puddings of different taste combinations at a rate of 672 cups per minute. The piston loading operation of the machine is controlled by a servo system from Siemens Energy & Automation ().
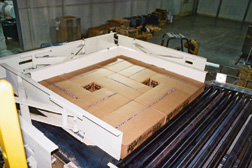
This thermoforming/filling/sealing process begins with the film for the cup being pulled from the film roll onto the machine as shown above. The stamped cup is placed on a conveyor belt.
The lid material is Pechiney's aluminum-plastic barrier coated multi-layer material that is pulled from the side onto the machine and sent to the sterile channel after both sides are sterilized. There, the air-filled side sealer attaches the sealing material to the filled and filled cup and continues to reach the sealing site, through a lower servo-driven closure disk and a higher pneumatic closure disk. Seal on each pudding cup.
After sealing, the cooling plate cools the lid, making it brittle and easy to cut. Then, the stamping machine divides the pudding cups into groups of 2, 3 or 6 groups according to the final packaging settings, and in each group, a scratch is made on the sealing film connected between the cup and the cup. It's easy to separate the pudding cups.
The finished pudding cup is transported to the conveyor and loaded into the handling device. Before leaving the filling workshop, the pudding cups on the two single-wire conveyors pass through a Lasetech laser encoder manufactured by Industrial Dynamics. The encoder prints the production date, product number, and best-edible date on the face of the pudding cup. And other information.
Gehl`s installed a 6400CE vertical stacker from the Hartness Dynac between the loader and the three wrappers, and between the wrapper and the two boxing machines. Divided into nine units, each unit can provide up to 439 inches high finished product. Mr. Gehl said: "These Hartness machines are the secrets to the successful operation of this line. We think this feature is very critical." As Gehl explained, this advanced-in-first-out package handling method consists of four The stacked function provided by the Dynac machine makes it easy for the company to track a batch of finished puddings with quality problems.
After the steps of filling, sealing, and coding, the pudding cups used in multi-cup combo packs leave the filling shop. They are transferred directly to the first group of Dynacs stackers, where they are piled up and later sent to three. On the Davis Sleeper, the paper label provided by Outlook Group () is wrapped onto the product.
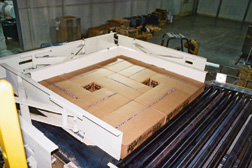
The Gehl`s system used two vertical stacking tables before its three traps.
Before the two packing machines also had such a stacking table, a total of four were divided into nine layers.
Each stacking unit provides up to 439 feet of stacking space.
After labeling, the multi-unit packaging group is brought to the second Dynacs stacking table, where the stacked product will be sent to two Douglas-made motor-driven WACP wraparound cartoners. The packing machine handles the product at a speed of 25 boxes per minute.
At the end of the packing step, the sealed boxes are then combined on a conveyor belt and sent to the Ultramark 3000 Series XJ-500 inkjet printer from Fas-Co Coders (). There, graphics including brand names and trademarks, product descriptions, ingredient details, box weights, number of products, best food dates, bar codes, and more were printed on the cartons at a print accuracy of 200 dots per inch.
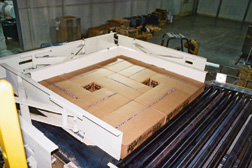
Cup lid made of aluminum plus plastic barrier coating
The box is then conveyed through a longitudinal bevel to a conveyor belt located high, and the conveyor belt transports the product to an elevated feed handling device by Currie. The system is fully automated, using an automatic tracking feed measuring conveyor belt, an independent power product steering and segmented transport components, a separate stripper tray operated by a bracket and pinion, and a power roller lifting bed. The pallets are loaded at a rate of 75 boxes per minute. The pallets it loads can be up to 40,348 inches long and up to 112 inches high.
Next, the palletized product is transported in a straight line to a Lantech Q1000 automatic rotary table stretch wrapper. The wrapped goods will then be sent out of the line waiting to be picked up by the lift operator. Before it is stocked, it has been installed
Gehl uses a brand new aseptic filling line produced by Hassia () USA. Mr. Mike Sowieja, Gehl's Deputy Director of Engineering, said: "This filling line allows filling 10 chocolate flavors and 14 vanilla-flavored pudding cups at a time; or 12 cups per flavor for each operation, with two flavors interspersed; If necessary, it can also be mixed with taste filling, layer filling, and cup filling, 4 cups, 6 cups or 12 cups, and because the production and packaging process is completely automated, the operating cost is relatively low."
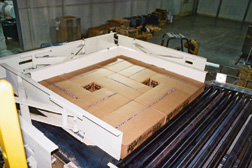
An automatic stacker above the ground transports the well-packed containers to a suitable location.
In order to form a new layer on the pallet.
This new packaging line includes four new Dynac vertical storage tanks produced by Hartness Intl. (), three Davis brand cartoners, and two packaged box loaders from Douglas Machine (). The Currie () tray machine and a rotary table stretch packer from Lantech () company are optimally configured to ensure the best product quality and maximum speed, and all of these require only two workers. The entire packaging line is integrated with the conveyors and consoles produced by Sentry Equipment ().
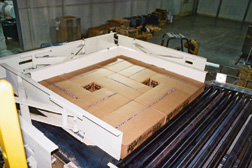
Place a separate aseptic molding/filling/sealing machine on its own
Easy to control temperature and other parameters.
A new measuring cup pudding complements Gehl`s original canned and bagged pudding packaging, offering an alternative to old customers. The main sales channel for new packaged products will be mainstream retailers, Mr. Gehl explained. “In the long run, customers who supply their own brands will be the main outlets for bulk products.â€
Gehl`s recently introduced this new set of equipment, Hassia's TAS type low acidity, steam anti-corrosion thermoforming/filling/sealing machine, with reference to the same equipment unit installed in the rival factory. Gehl said: "The difference is in operations," he added: "We feel that Hassia is the best company that can provide these devices."
Hassia TAS 16/80 is a sterile thermoforming/filling/seal system that was put into use at Gehl`s in February 2003. Its product width is up to 840mm and the production speed is 160mm per action. At Gehl`s company, the machine is horizontally arranged in two rows, each row is filled with 12 cups, so that each action can complete the task of filling 24 pudding cups, and can perform 28 filling operations per minute.
Unlike some other aseptic heat-setting/filling/sealing machines, this TAS 16/80 machine uses steam instead of hydrogen peroxide (hydrogen peroxide) to sterilize cup body and closure materials at room temperature. Save it. "With steam sterilization, you don't have to worry about hydrogen peroxide residue in the product," explained Jeffrey Martin, Gehl's special project manager, "Steam is a very clean disinfectant."
The new machine is placed separately so temperature and other parameters can be controlled. To take advantage of the versatility of the loader, Gehl`s installed two new aseptic storage tanks produced by Advanced Process Solutions (), each with a capacity of 3,000 gallons. The two tanks are responsible for transferring raw materials to the four buffer tanks of Hassia equipment, so that a series of pudding product combinations can be loaded at the same time. Although chocolate and vanilla-flavored products are currently being packaged, Gehl`s will also pack savoury cream, tapioca, chocolate and lemon-flavored puddings.
In order to prepare the pudding, pudding sauce was pumped from two 40,000-gallon storage tanks to a batch system. This system is also the product of APS. It first heated the pudding to a temperature for sterilization. - The chocolate taste is 281 degrees Fahrenheit, vanilla flavor is 276 degrees Fahrenheit - and then the pudding is cooled to 90 degrees Fahrenheit. At the end of this step, the pudding was transferred to a 3,000-gallon storage tank and from there the four buffer tanks of the filling machine were supplied.
This heat setting/filling/sealing process begins with the sheet material being used as the cup body material being pulled from the roll onto the machine. The upper end of the sheet is steam sterilized at 305.2 degrees Fahrenheit twice for 0.98 seconds each. . The body sheet is a five-layer material from Printpack (), which is a polyethylene layer/adhesive layer/oxygen barrier layer/adhesive layer/polyethylene layer from the inside out.
Next the cup body material enters the forming position where a stopper is first used to help the material to be preformed and then blown into the air to form a pudding cup. The molded pudding cup was sent to the filling machine. The filling machine used 24 loading heads to pack puddings of different taste combinations at a rate of 672 cups per minute. The piston loading operation of the machine is controlled by a servo system from Siemens Energy & Automation ().
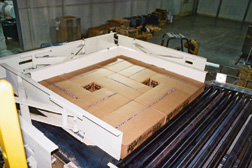
This thermoforming/filling/sealing process begins with the film for the cup being pulled from the film roll onto the machine as shown above. The stamped cup is placed on a conveyor belt.
The lid material is Pechiney's aluminum-plastic barrier coated multi-layer material that is pulled from the side onto the machine and sent to the sterile channel after both sides are sterilized. There, the air-filled side sealer attaches the sealing material to the filled and filled cup and continues to reach the sealing site, through a lower servo-driven closure disk and a higher pneumatic closure disk. Seal on each pudding cup.
After sealing, the cooling plate cools the lid, making it brittle and easy to cut. Then, the stamping machine divides the pudding cups into groups of 2, 3 or 6 groups according to the final packaging settings, and in each group, a scratch is made on the sealing film connected between the cup and the cup. It's easy to separate the pudding cups.
The finished pudding cup is transported to the conveyor and loaded into the handling device. Before leaving the filling workshop, the pudding cups on the two single-wire conveyors pass through a Lasetech laser encoder manufactured by Industrial Dynamics. The encoder prints the production date, product number, and best-edible date on the face of the pudding cup. And other information.
Gehl`s installed a 6400CE vertical stacker from the Hartness Dynac between the loader and the three wrappers, and between the wrapper and the two boxing machines. Divided into nine units, each unit can provide up to 439 inches high finished product. Mr. Gehl said: "These Hartness machines are the secrets to the successful operation of this line. We think this feature is very critical." As Gehl explained, this advanced-in-first-out package handling method consists of four The stacked function provided by the Dynac machine makes it easy for the company to track a batch of finished puddings with quality problems.
After the steps of filling, sealing, and coding, the pudding cups used in multi-cup combo packs leave the filling shop. They are transferred directly to the first group of Dynacs stackers, where they are piled up and later sent to three. On the Davis Sleeper, the paper label provided by Outlook Group () is wrapped onto the product.
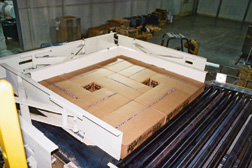
The Gehl`s system used two vertical stacking tables before its three traps.
Before the two packing machines also had such a stacking table, a total of four were divided into nine layers.
Each stacking unit provides up to 439 feet of stacking space.
After labeling, the multi-unit packaging group is brought to the second Dynacs stacking table, where the stacked product will be sent to two Douglas-made motor-driven WACP wraparound cartoners. The packing machine handles the product at a speed of 25 boxes per minute.
At the end of the packing step, the sealed boxes are then combined on a conveyor belt and sent to the Ultramark 3000 Series XJ-500 inkjet printer from Fas-Co Coders (). There, graphics including brand names and trademarks, product descriptions, ingredient details, box weights, number of products, best food dates, bar codes, and more were printed on the cartons at a print accuracy of 200 dots per inch.
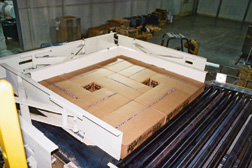
Cup lid made of aluminum plus plastic barrier coating
The box is then conveyed through a longitudinal bevel to a conveyor belt located high, and the conveyor belt transports the product to an elevated feed handling device by Currie. The system is fully automated, using an automatic tracking feed measuring conveyor belt, an independent power product steering and segmented transport components, a separate stripper tray operated by a bracket and pinion, and a power roller lifting bed. The pallets are loaded at a rate of 75 boxes per minute. The pallets it loads can be up to 40,348 inches long and up to 112 inches high.
Next, the palletized product is transported in a straight line to a Lantech Q1000 automatic rotary table stretch wrapper. The wrapped goods will then be sent out of the line waiting to be picked up by the lift operator. Before it is stocked, it has been installed
4 Person Sound Proof Meeting Pod
4 Person Sound Proof Meeting Pod,Acoustic Office phone booth, soundproof pod,Private Meeting Pod
Feat Top International(China) CO.,LTD , https://www.nbfeattop.com